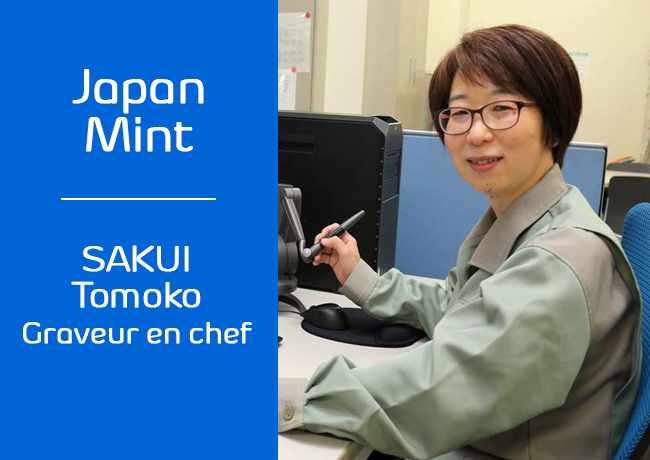
JAPAN MINT’s engraver SAKUI Tomoko – exclusive interview
- March 31, 2021
- by
- Pierre
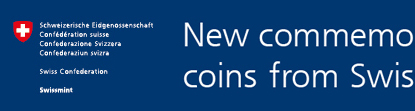
Japan has a long tradition of coins and medals engraving since over one century and a half. NUMISMAG wanted to make you discover the JAPAN MINT, where KANO Natsuo, first modern japanese engraver did work. Today it is a woman, SAKUI Tomoko, who is the chief engraver and head of design at JAPAN MINT. She granted us an interview.
NUMISMAG: What is the basic training of the Mint of Japan’s engravers?
JAPAN MINT: Firstly, we learn to make own engraving tools for modeling by ourselves. We make a wide variety of tools in different shapes and sizes from wooden and metal materials, which provide us a capacity to model exquisitely in the way we want.
Since our coin and medal production requires a precise model, we, the engravers, practice and learn skills over and over again such as a technique of effectively modeling a low relief that meets the manufacturing conditions and a method of duplicating and processing the model by making a plaster cast of it precisely, with guidance from senior engravers.
NUMISMAG: How many projects does the engraving workshop on in a year (average)?
JAPAN MINT: We work on about 20 projects a year that are organized by the Japan Mint. In addition, we make designs for commemorative coins, made-to-order products, etc.
NUMISMAG: How many full time engravers are there in the engraving workshop?
JAPAN MINT: There are 3 engravers in the Osaka headquarters and the Saitama branch each. Also, we have some designers in the Design and Engraving Division who are engaged only in designing of coins, medals, etc. and not involved in engraving.
NUMISMAG: Who was historically the first engraver of Japan Mint?
JAPAN MINT: The Japan Mint celebrates its 150th anniversary this year (2021) since 1871.
It was the engraver KANO Natsuo working in the Japan Mint at the time of establishment, who manufactured a western-style experimental coins as the first Japanese, and was engaged in designs and trial strikes and die making of the first modern coins.
He was born in Kyoto in 1828, started metal art training at the age of 12, and became an independent craftsman at 18 years old. At the age of 25, Natsuo moved to Edo (later renamed as Tokyo), was appointed to craft the sword equipment for Emperor Meiji in 1869. In the same year, he started to work for the Japan Mint. After the retirement in 1875, he became a professor at the Tokyo School of Fine Arts (the predecessor of Tokyo University of the Arts). Natsuo died in 1898.
KANO Natsuo, first modern engraver of JAPAN MINT
NUMISMAG: Did he create a tradition of modern japanese coin engraving Art?
JAPAN MINT: KANO Natsuo and his apprentice MASUDA Tomoo created designs of coins such as a new 1-yen silver coin, and moreover, they made a sample coin by hand carving. Thomas James Waters (1842-1898), a British architectural supervisor of the Japan Mint, applauded their fine workmanship and commented that there was no need to place an order for the coinage dies with the mint in Britain. Since then, Natsuo and his apprentices were entrusted with the designs and engravements of all of the coinage during the Meiji period.
NUMISMAG: What are the main sources of inspiration for the mint engravers?
SAKUI Tomoko (JAPAN MINT Special Officer for Design and Engraving): The design themes are offered by the Ministry of Finance and the product development department in the Japan Mint, so at first I gather general information in relation to the themes.
I visit places to look at something relevant like objects and sceneries, if possible.
Sometimes ideas suddenly come into my mind while I find inspirations from what I see and a music which I hear in my everyday life. Of course, coins from other mints may give me tips for my work. I often go to art exhibitions, but currently the pandemic of COVID-19 is forcing me not to attend many exhibitions casually.
Short Bio of SAKUI TOMOKO:
SAKUI Tomoko is Born in 1969. She studied hammering in metal art in the college and graduate programs. In 1996, She started to work at the Japan Mint. She is now Responsible for designing of coins and medals in the Design and Engraving Division. From October 2002 to July 2003, she studied abroad, at Scuola dell’Arte della Medaglia, in ROMA – Italy. There she learned the basics of coin design, relief engraving, direct carving of dies, waxwork and copper plate etching
From 2004 to present, she returned to the Japan Mint and works on engraving in the Design and Engraving Division. She is also involved in designing and modeling as needed.
SAKUI Tomoko, in the JAPAN MINT’s workshop
NUMISMAG: For example, what was their source of inspiration for National Treasure Medal “Jisho-Ji (Ginkaku-Ji)” released in 2020?
SAKUI Tomoko (JAPAN MINT Special Officer for Design and Engraving): The motifs on the obverse and reverse of the medal are decided as “The Kannon Hall” and “The Togudo Hall” located in Jisho-ji temple that are made of wood and listed in National Treasures of Japan, based on a request from the temple.
I visited the temple and walked around the garden for the purpose of reference to my work. I observed the scenery from different angles, hearing birds singing under the changing sunlight. The sand-mound gardens called Ginshadan and Kogetsudai are located in front of The Kannon Hall and I got inspired by the combination of their unique forms and the background architecture.
When figuring out a medal design, I always keep in mind to arrange motifs effectively in a round blank. This time, I could bring out something interesting by my design showing the well-balanced composition of the building and the gardens, so I gained a sense of achievement.
NUMISMAG: The Mint of Japan has been organizing for many years an international coin/medal engraving award. What were the reasons for the creation of this prize? What does it bring to the Mint of Japan?
SAKUI Tomoko (JAPAN MINT Special Officer for Design and Engraving): The Japan Mint has organized the International Coin Design Competition since 1998. The purpose of the event is to contribute to enhancement of the artistry of coin designs around the world by calling for design ideas from not only Japan but more widely overseas.
The Japan Mint believes that it also brings benefits to the Japan Mint itself such as improvement of design creativity and production technology, by being exposed to a lot of outstanding coin designs submitted from all over the world and manufacturing the medals featuring the designs awarded Most Excellent Work and Excellent Work.
NUMISMAG: Are some drawing and engraving works outsourced outside the Mint?
SAKUI Tomoko (JAPAN MINT Special Officer for Design and Engraving): The Japan Mint does not contract out drawing and engraving (However, there are some cases where designs and prototypes are brought to the Mint for made-to-order production, for example, the first and second prize medals of The National High School Baseball Championship of Japan.).
NUMISMAG: What do you think of the latest trends in the field of coin engraving such as high relief engraving (which has been honored for a few years by various mints around the world)?
SAKUI Tomoko (JAPAN MINT Special Officer for Design and Engraving): I think that motifs which give peace of mind and a sense of safety are preferred in the COVID-19 crisis.
NUMISMAG: What is the most memorable project that you have ever worked on?
SAKUI Tomoko (JAPAN MINT Special Officer for Design and Engraving): One of my most memorable projects is the New Zealand $1 Aoraki/Mount Cook silver commemorative coin program in 2007, which was the first foreign coinage struck by the Japan Mint after WWII, and I made the reverse design of the coin and engraved the original model. Although color coins by pad-printing are common nowadays, I remember that the Japan Mint just introduced the color pad printing technology to our coin production at that time. Honestly, I had a dilemma at first to add the color printing on the coin surface with delicate relief. But I found that the technology brought vivid color into the monotonous field of coin design and made it more impressive. That made me realize again how beautiful our product was.
Also, I was enjoyed creating the design of 2011 Children’s Song Coin Set featuring the poetry collections by KANEKO Misuzu, a Japanese children’s poet (1903-1930). The coin set was accompanied by Misuzu’s poetry collection book with illustrations, of which poems had been selected by our product development team. I was pleased to get an opportunity to handle the whole design of the coin set such as the design of the year medal and the packaging. I put all my focus on doing a rough sketch for the illustrations on the poetry book, and was trying to capture the images popping up in my thoughts when the poems were running through my mind.
As for the medal production, I was glad to be responsible for engraving the reverse of the medal depicting “Ootemari”, a double-petaled cherry blossom, in Cherry Blossom Viewing Series in 2006. The Japan Mint is famous for the cherry blossoms on its premises, and every year the President of the Mint chooses one cherry blossom for highlighting the year among more than 100 varieties. So, the Japan Mint produces and sells medals with engraving of the selected cherry blossom as Cherry Blossom Viewing Medals every year, and for the 2006 medal, I felt delightful to engrave cherry blossom beloved by many people.
Also, it was honor that my design was chosen as the victory medal of Nagano 1998 Winter Paralympic Games.
Moreover, last year, the member of the Design and Engraving Division were asked to design an anniversary logo for celebrating 150 years of the Japan Mint’s history and I was pleased that my design was adopted.
What I really feel the changes of the times from when I joined the Mint is the introduction of the 3D modelling method.
Now, it is absolutely essential for coin and medal production.
This 3D modelling method has come into use in the production of cloisonné medals (enameled medals) that is a major pillar of the product lineup of the Japan Mint. About 10 year ago, the original models for the medals were made entirely by hand, and that required enormous energy and time. But now that we can scan these models digitally and then, make concave part where the enamel can be applied by using the 3D modeling system, it takes less time for medal production.
The cloisonné medal that I involved in is “Awaodori” medal of the Japanese Festival Medal Series in 2015 (I did 3D modelling of it while another staff made the design and model.).
NUMISMAG: How do you see the future of coin engraving within the Mint of Japan and more generally in the rest of the world?
SAKUI Tomoko (JAPAN MINT Special Officer for Design and Engraving): I would say the tendency of high-variety-low-volume production will be developed by utilizing both engravings of clay modelling with hand tools and digital 3D modelling. I wish the variation of design motifs for engraving will be wider and free from restrictions, protecting the integrity of coins by more reliable anti-counterfeiting technologies.
We would like to thank SAKUI Tomoko and YANO Haruna, from Japan Mint, for their help to realize this interview.
Sources: Japan Mint and NUMISMAG